Flexible PCBs
The demand for flexible PCBs is increasing in all business segments with especially strong demands from medical and industrial markets.
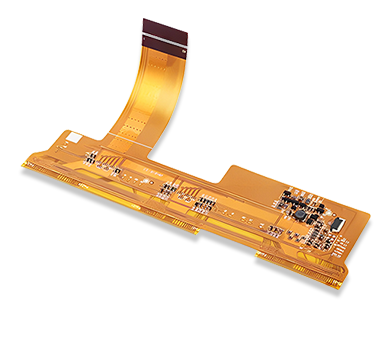
What are the available structures for flexible circuit boards?
There are numerous, different structures available. The more common ones are defined below:
Double sided flex (IPC-6013 type 2) Coverlay bonded onto both sided of an adhesiveless double-sided FPC core (two conductive layers) with plated through holes. With or without stiffeners.
Multilayer flex (IPC-6013 type 3) Coverlay bonded on both sides of an adhesiveless construction containing three or more conductive layers with plated through holes. With or without stiffener. Capability is 6L.
Feature | Technical specification |
---|---|
Number of layers | 1 – 6 layers |
Technology highlights | Mainly polyimide materials, flex PCB’s are necessary when motion of the PCB is needed, when 3-D interconnections are necessary (i.e. replacing cables and connectors) or when these are both combined due to limited available space |
Materials | Polyimide, Polyester |
Profile method | Laser cutting, punching, rout |
Copper weights (finished) | 8 μm – 70 μm |
Minimum track and gap | 0.05 mm / 0.05 mm |
FPC thickness | 0.05mm – 0.80mm |
Maxmimum dimensions | 250mm x 610mm |
Surface finishes available | OSP, ENIG, Immersion tin, Electrolytic gold, Gold fingers NiPdAu |
Minimum mechanical drill | 0.1 mm |
Why SprintPCB can Provide the most
competitive PCBs
Under the long-term strategic cooperation agreement with laminate supplier , the price we get is 10% cheaper than most competitors
PCB Inner / outer layers fab with LDI equipment, the automatic production reduce our labor cost 5%
Lean manufacturing increases product yield
About SprintPCB
We can provide competitive prices and guarantee the quality requirements of customers without excess quality. Our technical level can meet most of the industrial control and consumer products.
Manufacturing Equipment at SprintPCB
SprintPCB operate with most advance equipment in the industry to provide efficient production and high quality products with value added to our partners


Trusted by innovators since 2007
In the race to build tomorrow, SprintPCB engineers and PCB designers continually patent new technologies,
crossing design barriers—to help innovators bring new products to market.
"I am extremely satisfied with the quality of the PCBs you manufacture. The solder pads on each board are very smooth and the connections are very strong. I have worked with other manufacturers before, but the quality was always subpar. Since switching to SprintPCB, the quality of my projects has significantly improved. Thank you for your outstanding manufacturing process!"
- John Smith

Get High-Quality PCBs or PCBA at a Fraction of the Cost
Why Pay More for PCB Manufacturing?
Partner with Us for the Best Prices!
FAQ about Flexible PCBs
Flexible PCB is a type of circuit board that is made of a flexible material, such as polyimide or polyester, instead of traditional rigid FR-4 material. It allows for greater design freedom and can be bent, folded, and curved to fit into tight spaces.
Flexible PCBs have many benefits, including increased design flexibility, reduced weight and size, increased reliability, improved performance, and cost savings compared to traditional rigid PCBs.
Flexible PCBs are widely used in many applications, including mobile devices, wearable technology, medical devices, and automotive electronics.
Flexible PCBs are typically made from polyimide or polyester, which are flexible and have good thermal and electrical performance. Other materials, such as polycarbonate, may also be used depending on the specific requirements of the application.
Flexible PCBs are made entirely of a flexible material, while rigid-flex PCBs are a combination of flexible and rigid PCBs. Rigid-flex PCBs are used in applications where a combination of flexibility and rigidity is required, and they offer the benefits of both flexible and rigid PCBs.
CONTACT US
We would love to respond to your queries and help you succeed.
During our business Hours: 9:00~18:00