Metal substrate
Metal substrate is growing rapidly and supporting sectors including automotive, medical, aerospace, lightning applications and industrial controls.
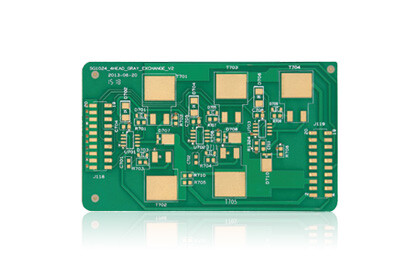


New opportunities with insulated metal substrate
For greater amounts of energy or local thermal loads, e.g in modern constructions with high intensity LEDS, IMS technology can be used. The abbreviation, IMS, stands for “Insulated Metal Substrate.” This is a PCB built on a metal plate – normally aluminium – on which a special prepreg is applied, the primary qualities of which are an excellent capacity for heat dissipation and great dielectric strength against high voltages.
Feature | Technical specification |
---|---|
Number of layers | 1 – 4 layers |
Technology highlights | Effective heat sink solutions for thermal applications. This construction type enables superior heat dissipation through use of either aluminium or copper substrate bonded to the insulated circuitry through thermal pre-preg or resin systems. Breakdown Voltage 3KV /5KV |
Materials | Aluminium & copper plates |
Dielectric thickness | 0.05 mm – 0.20 mm |
Thermal conductivity | 1-12 W/m/K |
Profile method | Punching, Liquid cooled routing |
Copper weights (finished) | 35 μm – 140 μm |
Minimum track and gaps | 0.10 mm / 0.10 mm |
Metal core thickness | 0.40mm – 3.20mm |
Why SprintPCB can Provide the most
competitive PCBs
Under the long-term strategic cooperation agreement with laminate supplier , the price we get is 10% cheaper than most competitors
PCB Inner / outer layers fab with LDI equipment, the automatic production reduce our labor cost 5%
Lean manufacturing increases product yield
About SprintPCB
We can provide competitive prices and guarantee the quality requirements of customers without excess quality. Our technical level can meet most of the industrial control and consumer products.
Manufacturing Equipment at SprintPCB
SprintPCB operate with most advance equipment in the industry to provide efficient production and high quality products with value added to our partners


Trusted by innovators since 2007
In the race to build tomorrow, SprintPCB engineers and PCB designers continually patent new technologies,
crossing design barriers—to help innovators bring new products to market.
"I am extremely satisfied with the quality of the PCBs you manufacture. The solder pads on each board are very smooth and the connections are very strong. I have worked with other manufacturers before, but the quality was always subpar. Since switching to SprintPCB, the quality of my projects has significantly improved. Thank you for your outstanding manufacturing process!"
- John Smith

Get High-Quality PCBs or PCBA at a Fraction of the Cost
Why Pay More for PCB Manufacturing?
Partner with Us for the Best Prices!
FAQ about Metal substrate PCBs
A Metal Substrate PCB, also known as Metal Core PCB, is a type of printed circuit board that uses a metal base material, typically aluminum, as the substrate instead of the traditional FR-4 glass-reinforced epoxy resin.
Metal Substrate PCBs offer several advantages such as improved thermal management, increased durability, and better mechanical stability compared to traditional PCBs.
Metal Substrate PCBs are commonly used for high-power applications such as power electronics, lighting, and industrial control systems due to their improved thermal management capabilities.
The main disadvantage of Metal Substrate PCBs is their higher cost compared to traditional PCBs. They can also be more difficult to manufacture due to the metal substrate and require specialized equipment and materials.
CONTACT US
We would love to respond to your queries and help you succeed.
During our business Hours: 9:00~18:00